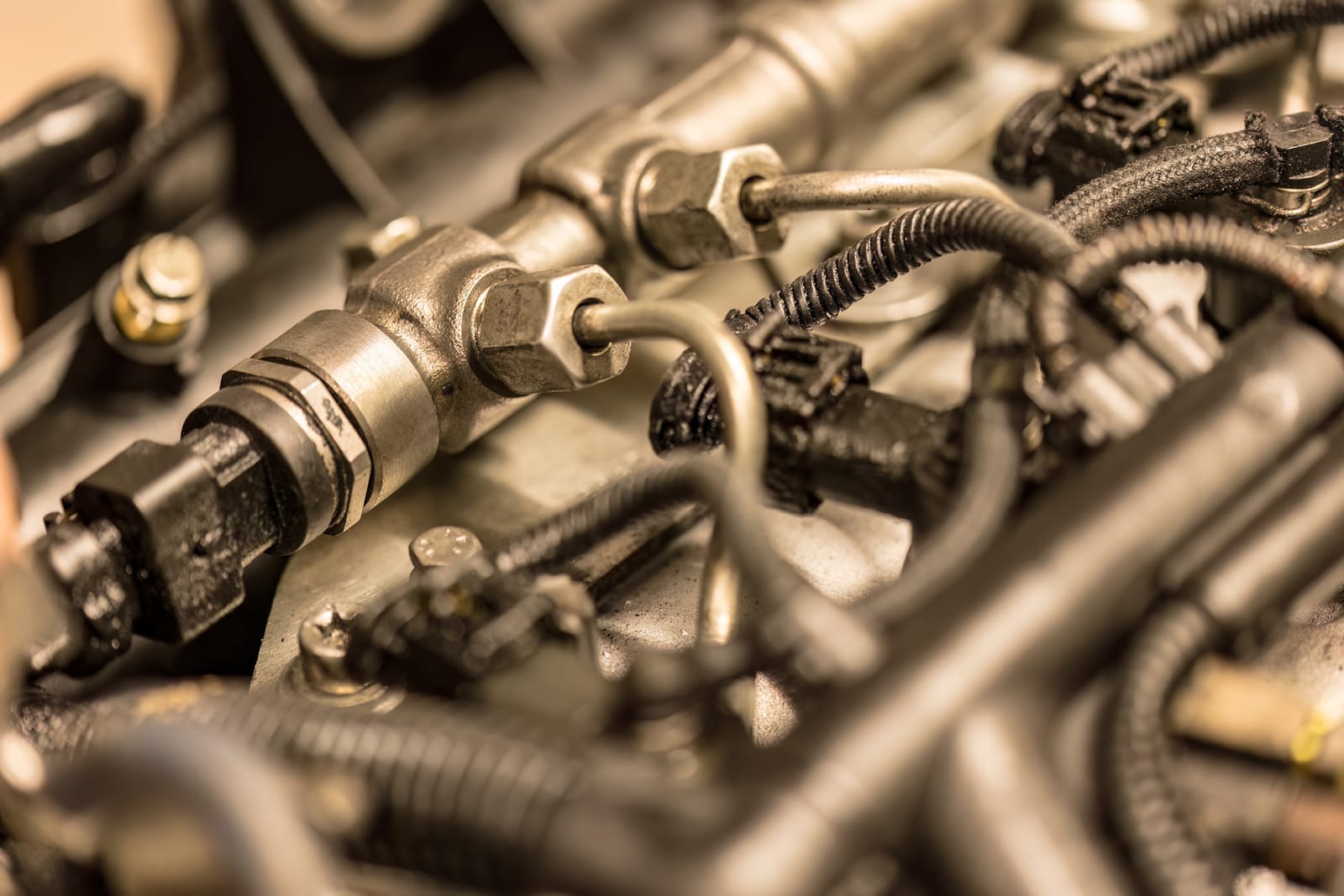
Supplier Quality Manager in the automotive industry (injection systems)
Term:
2022/01 – 2022/05
Interim quality manager in the metal industry
Area of responsibility: 25 employees
Branch:
- Metal industry
- Door closing systems
Turnover:
- 95 million €
Employees:
- approx. 650
Situation in the company:
- The quality manager in permanent employment was terminated in a flash, he was immediately released from his duties
- Handover took place by the management
Country:
- Germany
Order:
- Responsibility for quality management in the plant (production, customers, suppliers, projects)
- Leadership and further development of subordinate employees
- Responsibility for the continuous improvement of the QM system, methods and strategic orientation
- Problem analyses and coordination of the error correction process in close cooperation with internal departments, customers and suppliers
- Ensuring the quality of mechanical, electronic and electromechanical components and systems as well as integrated digital components / systems
- Development of quality concepts for new projects and series
- Development of a sustainable quality strategy / recommendation for action on the basis of a weak point analysis with the focus on organization, processes, products and employees.
Measures:
- Sensitization and training of employees through background information and lived error culture
- Activities within the scope of personnel responsibility incl. Job interviews
- Preparation of a 3-year strategy for personnel (training, transfer, increase, exchange, change), organization (insertion of new structures and responsibilities) and technology (increase of machinery) incl. Key figures
- Regular reporting (reviews) to the management board
- Cross-plant topics (procurement guideline, 8D report, special releases, advance quality planning (APQP), presentations, workshops) in coordination with the other Q managers
- Invitation of the sister plant for the purpose of joint reduction of defective deliveries and components
Successes:
- Reduction of complaints by about 20%
- Increased understanding of error culture and transparency created
- Reduction of special releases
- Synergy effects in other departments and between plants
Special challenge:
- Build trust with employees, guide, challenge and encourage them
- Preparation of various reports (documents deleted by ex-employee)
- Involvement of the team in the preparation of reports and management reports. (In the past, team was not involved).
- Communication and understanding between plants was strained